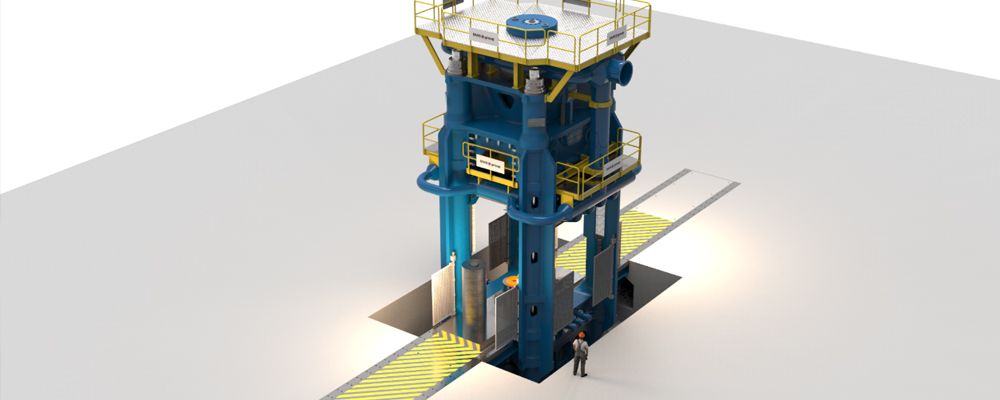
Aubert & Duval invests in SMS group closed-die forging press for manufacturing innovative forgings
- 75 million euros to be invested in new forging technology for the total project
- Long-standing partnership confirmed
- Special applications for the aerospace industry
- New materials and processes for high-performance applications for the aerospace industry
On January 15, Aubert & Duval placed an order with SMS group in Mönchengladbach for a hydraulic closed-die forging press for its Pamiers site in Ariège, France. The contract is at the heart of the company’s vision to make Aubert & Duval a leading European metallurgy company, particularly in the fields of aerospace, energy, and defense and to be prepared for the next generation of aircraft.
The four-column, hydraulic closed-die forging press to be supplied by SMS has a forging force of 60 MN. Going forward, this will enable Aubert & Duval to produce particularly precise forgings, such as turbine disks, shafts and structural parts.
The modular structure of the hydraulic press means it can accommodate an isothermal forging module, which Aubert & Duval will use in future to manufacture high-performance components for aircraft and engines based on vacuum powder metallurgy.
The force-transmitting telescopic cylinder is driven by frequency-controlled pumps that can be switched off. This provides for energy-optimized press control with three press force stages (20, 40, and 60 MN). What’s more, the press is equipped with extensive sensor technology for future digitalization, and is thus ready for Industry 4.0.
The press is scheduled to go into operation in 2027 and will replace an older Schloemann closed-die forging press supplied by SMS, which was built in 1932. Thanks to the new, state-of-the-art robot environment, the new press will be better integrated into the existing production infrastructure.
The new plant contributes to achieving Aubert & Duval’s decarbonization targets, as it operates in a far more energy-efficient way than the old facility. Not only that, the forgings that the press can manufacture allow the turbines to be designed more cost-effectively and with a higher level of performance, leading to a significant improvement in the efficiency of the turbines.