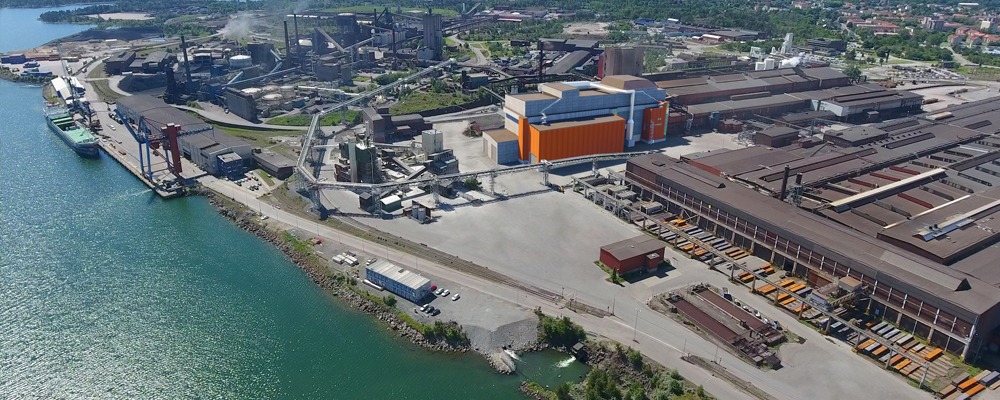
Groundbreaking ceremony in Sweden to decarbonize the steel industry
SMS group to build new electric arc furnace for SSAB for fossil-free steel production SMS group and SSAB are paving the way for a cleaner, more efficient, and environmentally friendly steel industry in Sweden SSAB will use an AC-EAF as part of its plan to decarbonize its steelmaking production process The new 190-ton EAF will be one of the largest installations in the world SMS group has secured the contract from Nordic steelmaker SSAB to engineer, deliver and construct a new electric arc furnace (EAF) for steelmaking at SSAB’s site in Oxelösund, Sweden. The scope of supply includes a 190-ton Alternate Current-Electric Arc Furnace (AC-EAF) capable of processing various raw materials, including fossil-free Direct Reduced Iron (DRI) or Hot Briquetted Iron (HBI), and scrap. With an upper shell diameter of 9.3 meters, the new EAF is one of the largest installations in the world for similar applications, and it will help SSAB to scale up the decarbonization of its production processes. SSAB is revolutionizing steelmaking with two unique steels with virtually zero fossil carbon emissions: SSAB Fossil-free and SSAB Zero. SSAB Zero is based on recycled steel and SSAB Fossil-free is based on sponge iron reduced with hydrogen instead of coke coal. Both are heated in EAFs powered by fossil-free electricity and other fossil-free fuels. SSAB’s ambition is to be a virtually fossil-free company in around 2030. SMS will supply all automated features including the slag handling and Eccentric Bottom Tapping (EBT) operations, the advanced electrode control X-Pact® SynReg, which, together with advanced robotics applications, such as the X-Pact® Sampler, ensure operational safety as well as better precision and productivity without human intervention. The automation system for the new plant is setup in the X-Pact® Plug & Work test center from SMS in Germany, connected with a virtual process and production simulation. This concept of integration testing allows for a shorter ramp-up, high product quality and a stable production environment. During the X-Pact® Plug & Work integration test, SMS experts will provide training for SSAB's personnel. The implemented process control and automation ensures a reliable "tap-to-tap time" (t-t-t), resulting in lower energy consumption and high production efficiency. The new EAF will produce high-quality liquid steel, facilitating SSAB's smooth transition from the integrated route to the electric route without significant disruptions. Side-wall burners, lime/carbon injectors and off-gas analyzers guarantee optimized chemical energy utilization. The scope of supply further includes an unparalleled yard management system for plant-wide raw material handling with efficient tracking and noise reduction thanks to an exceptionally large number of special containers. The project also represents an extension order to the Manufacturing Execution System (MES), which is currently been implemented at SSAB by SMS. In addition, SMS group's digital twin for SSAB, which includes Genius CM and DataXpert, will provide the digital representation of the EAF and serve as a central interface for predictive maintenance. “The collaboration between both companies represents a pioneering step towards a sustainable and environmentally conscious steel industry. By integrating innovative technologies and using fossil-free materials, the companies are demonstrating their commitment to reducing CO2 emissions and leading the industry towards a greener future,” said Olaf Stalfort, Chief Sales Officer Region Europe for SMS group.