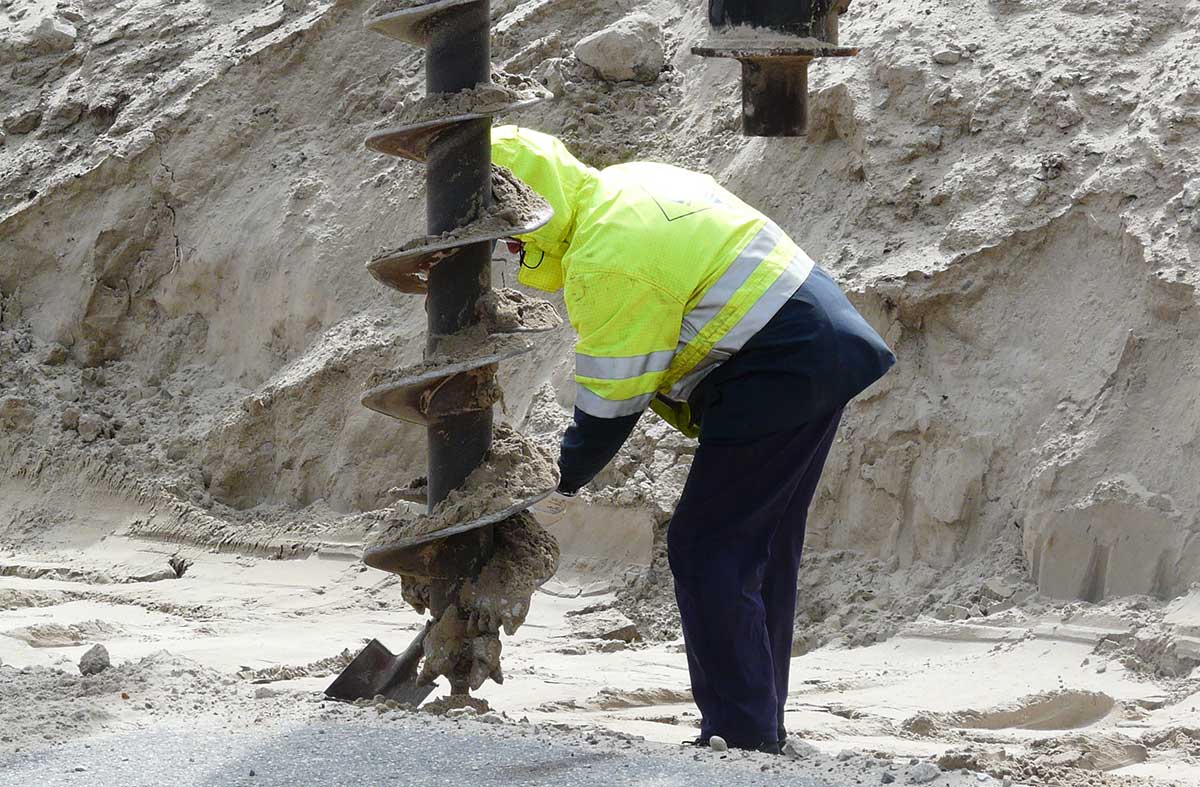
Geothermal energy recommends itself warmly
Valves used in the geothermal sector need to be as tough as it gets. In the past, many pumps failed to cope with the hostile environment of this form of energy production, causing tremendous costs. Today, the sector is transforming. Special valves are being produced in series that can make use of geothermal heat.
All signs point towards global growth for geothermal energy – and on a major scale. Many countries will “being to make use of geothermal energy, others will continue to expand this form of energy,” predicts the Bundesverband Geothermie (BVG), the German Geothermal Association.
Global growth
In 2015, worldwide heat production grew 39 percent compared to 2010, according to the “Country Reports”, to a total of ca. 70,300 MWt (megawatts thermal). China even doubled its installed capacity to around 17,900 MWt. India recorded growth of 272 percent to nearly 1,000 MWt in the same period, while the USA grew 38 percent to ca. 17,415 MWt, France 74 percent to around 2,350 MWt and Germany by 14 percent to 2,850 MWt. Thailand grew strongest, namely 5,060 percent, which brought capacity to “just” 129 MWt.
Worldwide geothermal power capacity also grew from 2010 to 2015, albeit not as strongly. Geothermal energy production grew by 16 percent to a total of 12,600 MWt installed capacity. In the USA, geothermal energy advanced 11 percent to 3,450 MWt, in Mexico by 6 percent to slightly above 1,000 MWt, in Kenia by 194 percent to around 600 MWt, in Germany by 280 percent to 27 MWt, while Italy here increased by 9 percent to nearly 920 MWt. Today, geothermal power plants can be found in 24 countries around the globe, generating energy from heat.
Constant availability
Demand for geothermal energy is growing in Germany, due to the energy transition. Geothermal energy is supposed to augment the mix of renewable forms of energy, generated by solar and wind power. Germany has already embarked on its path – 30 plants are currently in planning, two are being constructed and four will serve as research projects. They will expand on the 33 plants already in operation. Geothermal energy has a major advantage compared to other forms of renewable energy, namely “that it is constantly available, regardless of weather conditions or the time of day or year,” as the Munich City Utilities (SWM) state.
The time has thus come for change, as all sectors connected to geothermal energy recognised several years ago. In the past, operators of geothermal power plants were forced to use pumps for oil and gas industries, which weren’t designed to meet the requirements of geothermal energy. “Compared to the crude oil sector, pumps used for geothermal energy have to date been not very efficient, and show signs of wear at an early stage,” reports BINE Information Service, published by the FIZ Karlsruhe – Leibniz Institute for Information Infrastructure GmbH, which is in parts funded by Germany’s Federal Ministry for Economic Affairs and Energy (BMWi). There were no special pumps available for geothermal applications.
Valves prone to failure
As such, pumps were highly prone to failure, some pumps already broke down after just a couple of months. In the Unterhaching geothermal power plant, ten ESP pumps (electro-submersible pump) had “given out”, as VDI Nachrichten, the news service of the The Association of German Engineers (VDI), reported several years ago. More often than enough, broken frequency converters, bearings, damaged bearings or hot windings were to blame. “These failures really cost money”. Around one million euro need to be invested, per pump.
Not only the technology, but also the dimensions make pumps for geothermal applications a very expensive component. The rather new pump in the Freiham geothermal plant is 45 metres long, and has a total weight of 45 tons, including the rod. A heavy-duty crane was needed to lower it 600 metres below the surface. Here, the pump conveys thermal water with a temperature of approximately 90° Celsius from a depth of 2,500 metres to the surface.
High temperatures, aggressive gases
The production depths alone indicate the conditions pumps have to cope with, and make understandable, why pumps from the oil and gas industry aren’t the best of choices. High temperatures and feed rates, aggressive gases and crystallised salts demand an optimal performance from pumps.
Solutions need to be found for special pumps in geothermal applications – numerous manufacturers are working vigorously on hard-wearing components. Baker Hughes is one such example. The manufacturer of special geothermal pumps constructed a high-temperature test loop on its company site, in order to test entire pump systems under real-life conditions. “Field tests have yielded further insights into structural weak points in the aggregates used to date,” reports BINE in its Projektinfo 3/2016. Scientists had salvaged broken pumps from German geothermal plants, taken them apart and analysed the causes of defect. “On the basis of this data, they then developed modified prototypes which promise significantly higher efficiency and a longer service life”. Here, they concentrated on the conditions found in hydrothermal plants in South Germany, where thermal water reaches temperatures between 120 and 140° C, and is highly calciferous. Baker Hughes collaborated with the geothermal plants in Oberhaching, Dürrnhaar, Sauerlach, Grünwald and most of all Unterhaching for this task, reports BINE.
Temperature and pressure fluctuations
With hardly any lubricant properties and containing dissolved lime, the thermal water can have grave consequences for components. The limestone “is then deposited on all components, particularly the hotter bearings. These deposits prevent lubrication and cooling of the bearings, which then leads to overheating and destruction of the pump shaft,” explains BINE. To make things worse, a layer of limescale acts as insulation, preventing heat dissipation from the motor.
“The high absolute water temperatures and the cyclical temperature and pressure fluctuations which arise when the plant is at a standstill or operates at a reduced capacity are a source of stress for pump bearings, seals and motor insulation. “Thermal water furthermore contains dissolved gases. During the course of time, these diffuse into the oil with which the motor is filled. When a pressure drop occurs, the volume of the gases increases and pushes the oil out of the motor”.
Redesigned bearings structure
In general, the pump rates in geothermal plants vary – depending on the current heat demands of the plant and heat grid. “As a result, the pumps are frequently subject to start and stop procedures or phases with reduced capacity,” explains BINE. As such, the resulting variation of torque, motor temperature and pressure cause extra stress. In order to monitor pumps deep below the surface and initiate maintenance early enough, measurement sensors are required that can withstand high temperatures, and can transfer a large number of variables with a high data transfer rate.
In the end, the outcome was positive. The motor’s bearings structure was entirely redesigned – and there have been no more failures. “A pump with optimised bearings has been operating in a southern German plant for over 8 months without any failure occurring. The weak points found to date in the insulation have been rectified,” states the news service.