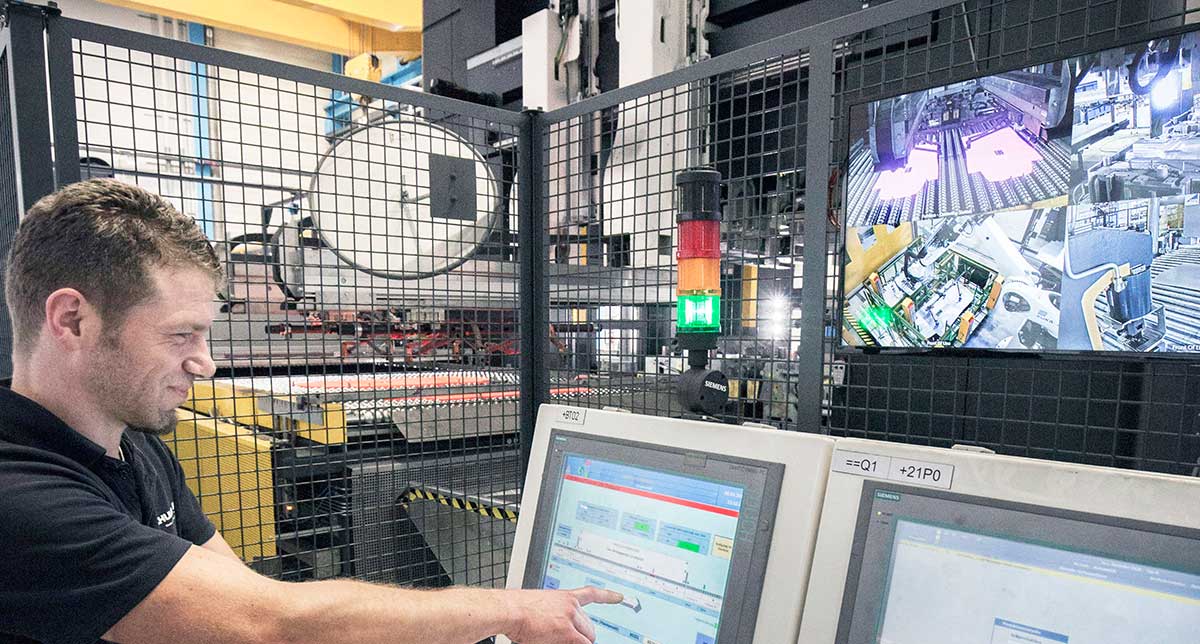
Smart Press Shop live
At the EuroBLECH trade fair, Schuler will demonstrate solutions for digitalization and networking on its new MSP 400 servo press
At the last EuroBLECH in Hanover in 2016, Schuler unveiled the Smart Press Shop, its vision for a digitally networked intelligent press shop. At this year’s EuroBLECH, the world’s leading trade fair for sheet metal working, the specific benefits of forming technology solutions in the age of Industry 4.0 (the Industrial Internet of Things, IIOT) will be on display with the theme “Discover the Digital Today” at the Schuler exhibit (located at Stand F82 in Hall 27). Schuler’s main exhibit display will be made of genuine iron and steel—its new MSP 400 servo press—and will give visitors an opportunity to experience intelligent software applications like the Smart Assist and the Optimizer.
“The digital transformation of the press shop is already well underway,” says Domenico Iacovelli, Schuler’s CEO since April 2018. He adds: “At EuroBLECH, we will demonstrate that both major automakers and medium-sized suppliers can use the Smart Press Shop for more efficient production and fewer rejected parts. This means that we can give them the competitive edge they need—true to our motto for this year’s event: Ready to Win Together.”
As an added highlight, Schuler will also use EuroBLECH to showcase the latest innovations in servo press lines and hydraulic presses, as well as new developments in automation and transfer technology. Die specialist AWEBA will be on hand at the neighboring stand (E82) to present its wide range of products and extensive engineering expertise in the areas of forming, blanking, fine blanking, and hydroforming. Backed by its subsidiary AWEBA, Schuler has the distinction of being the world’s only supplier of presses and automation as well as dies used to manufacture motors for electromobility, the latter of which will also be a focus of Schuler’s exhibit at the event.
Enhancing overall equipment effectiveness
Schuler has also already demonstrated its ability to fully network different production facilities with its systems for constructing large-diameter piping (“Pipe ID 4.0”) and train wheels. Among other things, this process requires the availability of data necessary for determining and increasing the overall equipment effectiveness (OEE). The data is prepared by the system so that a quick glance is all it takes for the production manager to determine the total number of parts produced, how many of these parts are acceptable, and which shift had the best performance.
The collected data also serves as a basis for functions like the tracking & tracing of safety-related parts. Among other things, the system links these parts to information about the starting material used and the material’s origin, about the system’s lubrication and drawing force, and about other production conditions. All of this makes it possible to provide a complete trail of documentation in the event of quality-related complaints.
To monitor the condition of individual components for changes, wear, or damage (a feature referred to as condition monitoring), Schuler is integrating more and more sensors into its machines; such as those which measure vibrations and temperatures, for example, so that this data can be intelligently processed and displayed. Currently, a large-scale field test is in progress in Göppingen involving a 1,600-ton hydraulic die hardening press, which produces parts for lightweight automotive construction from sheet metal heated to 930 °C. A live feed from the Hot Stamping TechCenter is planned for this year’s Schuler exhibit.
Virtual training for operators of press lines
EuroBLECH visitors will also be able to catch a glimpse of the new virtual training system from Schuler’s Forming Academy. It serves as a basic training of the operators dealing with the real forming systems in the press shop. This takes place in virtual space while a new system is being put into operation or the production is already running. Thus, the production in the press shop is not disturbed and the operators can be optimally prepared.
“Schuler is putting forming technology on the fast track to the digital future,” notes CEO Domenico Iacovelli, who then offers a comparison to bobsledding: “We provide the initial push, but the customer handles the technically advanced equipment.”