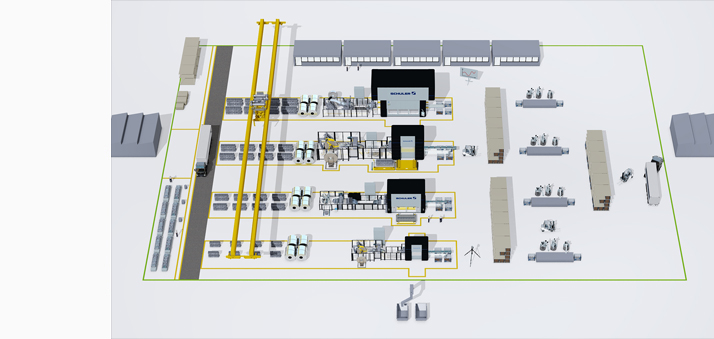
The transparent press plant
With the Machine Monitoring System, Schuler is presenting a comprehensive model for system monitoring at the EuroBLECH trade fair
We can’t see into a press, if we could it would avoid so many unplanned downtimes, if, for example, a faulty part could be identified sooner. However, the Machine Monitoring System (MMS) of the future, which Schuler will be presenting a model of at the EuroBLECH trade fair, provides completely new insights into presses: With the aid of comprehensive system monitoring, availability can be increased, production and parts quality can be improved, and energy consumption can be lowered. The MMS is part of the Smart Press Shop, a collection of Schuler solutions for networking in the field of forming technology.
Rapid fault analysisSchuler’s model for system monitoring combines a variety of existing solutions. An integral part of the MMS is the intelligent diagnostics, which automatically archives and evaluates physical variables and control states when specific events occur. This enables rapid fault analysis.
The state monitoring function monitors the system at regular intervals for damage and wear, using torque curves and structure-borne noise analyses, for example. Thanks to this state-based maintenance, components only need to be replaced when they have actually reached the end of their life, and not just because they have been in operation for a specific amount of time.
Improved process reliabilityWhen it comes to process monitoring, the focus is on machine protection. Permanent logging of parameters such as press force or vibration progression enables a cycle-accurate response in real time, where necessary. Process reliability is thereby also improved.
Energy monitoring involves recording and evaluating all measured variables which are relevant for energy efficiency and network quality, such as power consumption, voltage dips or harmonics. This means that not only can system operators save energy costs, in some circumstances they can also obtain investment grants and favorable loans.
Increased total system effectivenessThe production data acquired includes all planned and unplanned downtimes including their causes, fault messages, target/actual production and the quality of the parts. In this way, the system operators gain an overview of the production status and a basis for calculating the overall equipment efficiency (OEE).
Last but not least, all quality-relevant data is recorded and archived for each part produced. This enables the manufacturer to provide the necessary proof for items such as safety parts.