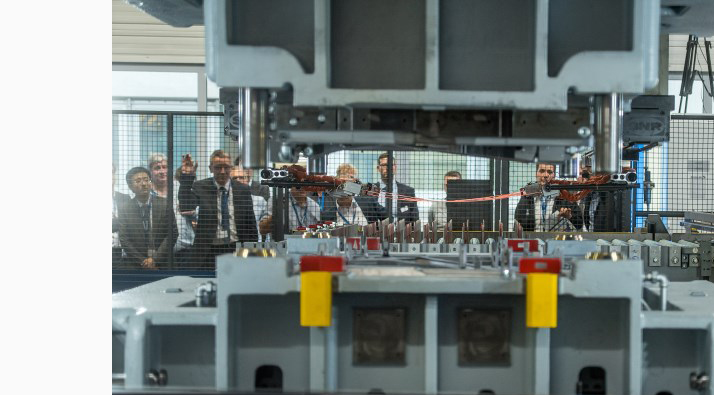
Customers thrilled by Hot Stamping TechCenter
More than 150 visitors experience cuttinge-edge hot stamping press with an output capacity of 7.5 strokes per minute
7.5 strokes per minute, up to four parts per stroke at a reproducible high quality: Schuler customers have experienced the reliable and economic production of high strength components at the end of September in the Hot Stamping TechCenter. More than 150 visitors had come to the research and demonstration center in Göppingen, Germany, which features a 1,600 ton hydraulic press with PCHflex technology, compatible die, roller hearth furnace and Twin Feeder automation.
“Our customers have been completely thrilled by the Hot Stamping TechCenter”, says General Manager Dr. Martin Habert, who heads the Hydraulic Division at Schuler. “One of the visitors even took a produced part with him in order to verify the accuracy himself. We gladly gave him the part, because we know the high precision our technology offers.”
Car manufacturers use more and more hot stamped parts because they offer a high strength and a low weight. Today, hot stamped A- and B-columns as well roof frames or connecting plates can be found in almost every new car. According to experts, the demand will double to 600 million pieces by 2020.
Schuler’s PCHflex technology allows faster cooling of the parts – which are heated to 930 degrees Celsius – because the contact pressure is distributed more evenly. This increases output performance significantly and ensures a more robust process with consistently high component quality. Conventional hot stamping dies can also be used on PCHflex lines for alternate and start-up production. Thus, the line in the Hot Stamping TechCenter is available for die tryout and the production of small batches for Schuler customers.