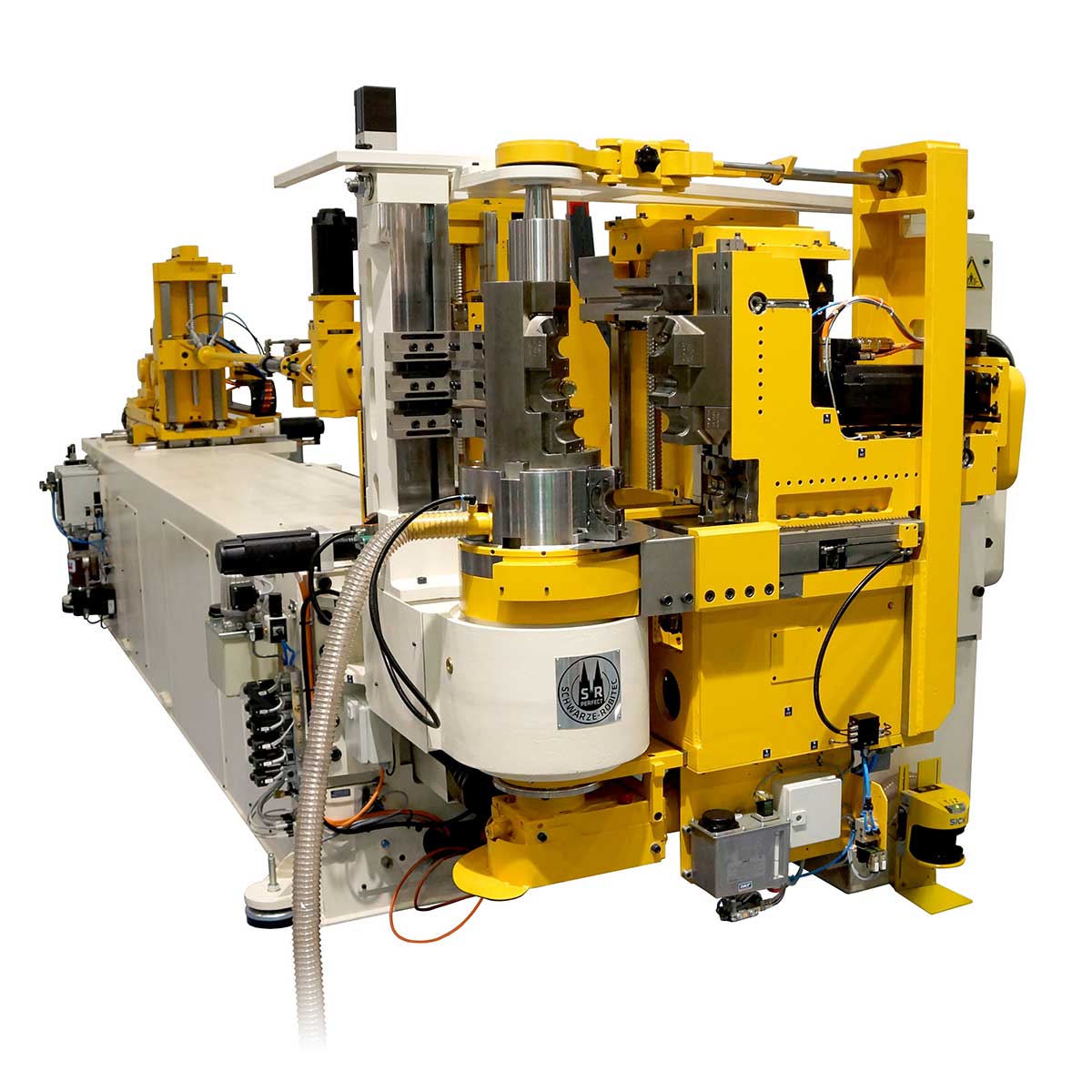
Schwarze-Robitec at Fabtech: Combined tube bending expertise
For the automotive sector, high-volume production is crucial: each step in the manufacturing process is tailored towards speed and an efficient use of material resources. And it is with these requirements in mind that Schwarze-Robitec has fine-tuned and continuously developed tube bending machines for this sector. The German manufacturer recently showcased its technology at the US metalworking trade fair Fabtech in the form of its fully equipped, fully electric multi-radius tube bending machine, CNC 80 E TB MR.
The CNC 80 E TB MR from Schwarze-Robitec's High Performance series is capable of bending tubes with diameters of up to approx. 3 inches (80mm) and can also cut them in the same process step thanks to an integrated fully electric cutting unit. At Fabtech, the German machine manufacturer had presented the fully electric version of this feature to a US audience for the first time. By combining bending and cutting processes, the machine enhances efficiency and saves resources during processing, leading to shorter turnover times and up to a 90 percent reduction in material waste. Despite featuring a multi-stack bending tool, the machine is able to cut tubes directly thanks to its extended vertical transport carriage. A vertically adjustable pressure die moves to the individual levels in sync with the tube. This means that the contact pressure can be optimally gauged, while tool costs and tool changing times are reduced.
Furthermore, additional features of the machine help to ensure an even faster production process. For example, for each bending sequence the intelligent NxG control system assesses the interaction between all axes, operates them simultaneously and prepares the next sequences. This reduces production time by 20 to 40 percent depending on the component and the desired tube geometry. In addition, faster refitting times are ensured thanks to the Quick-Tool-Unlock system in combination with a rapid clamping system for the bend former. The tension bars can thus be opened and closed with ease for tool changing, whilst no bolts are required to fasten the bend former to the turntable. This helps to increase repeatability and process security.
Schwarze-Robitec has perfected this machine through numerous refinements, such as a freely stored bend former. Fabtech trade fair visitors in Chicago were able to witness a highly efficient tube bending process up close.