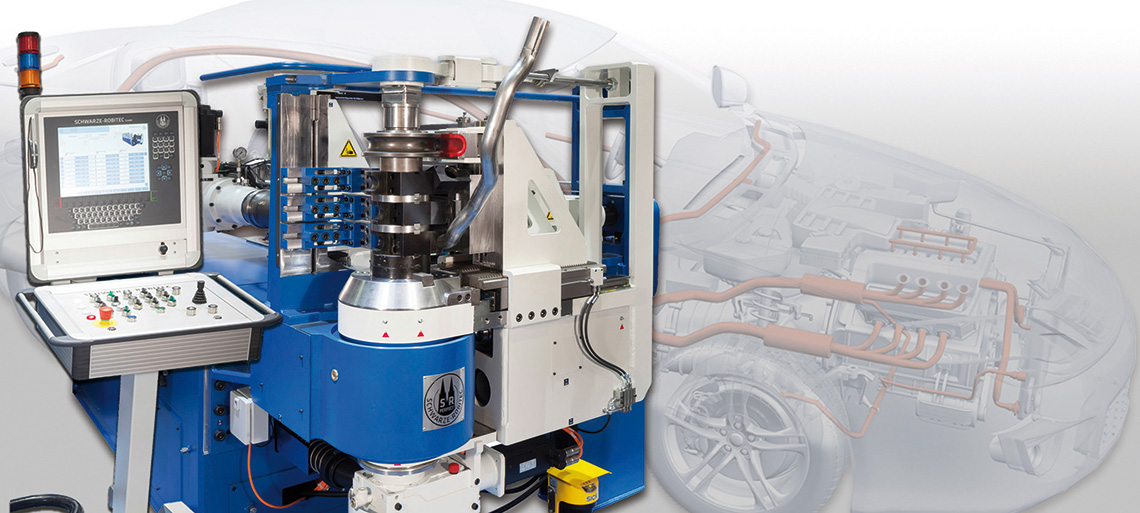
Resource efficiency in the supplying industry
Bert Zorn, Managing Director of Schwarze-Robitec, on the subject of resource-efficient tube bending technologies.
Subjects such as sustainability and green technology have been discussed in the media for several years or serve as popular anchor for company reports. Nonetheless, the reality in industry is still not consistently sustainable because producing enterprises use the major part of the gross production value for material. According to calculations by the German Federal Statistical Office this is an average 45 percent. The upshot of this is a major savings potential, both for sustainability and the operating costs of companies. In the light of rising costs for raw material and energy, one thing is sure, however: Those wishing to stay competitive need to use resources sparingly, streamline production processes and thereby increase efficiency. The resource ‘human’ should also be taken into consideration comprehensively in this context because operator-friendly and safe production processes make a major contribution towards profitability of companies.
Reduced lubricant and energy consumption
For large-scale production of tubes, the dosage of lubricants harbors a significant savings potential with regard to material. Lubricants counteract the high tribological loads on tool and work piece which occur during cold bending. With most lubrication methods, the lubricants are introduced into the tube to be bent in large quantities. To remove the lubricants from the bent tube after forming, they need to undergo an elaborate cleaning process where further chemicals are used. Automatic lubrication systems achieve a far lower consumption. With the help of compressed air, they only moisten the bending mandrel surface and inner wall of the tube. As a result of this optimal dosage, both the costs and the effort for the subsequent cleaning of tube and machine are considerably reduced.
The micro-lubrication from Schwarze-Robitec works according to this principle. For this procedure, the lines for oil and compressed air pass through the mandrel rod all the way to the mandrel, where the oil is dispersed by the compressed air. During the bending process it exits from the mandrel through small drill holes. This way, the system combines an appropriate lubrication with minimal lubricant consumption. Saving resources not only means reducing the use of material, but also the use of energy. Useful means are, for example, energy recovery modules or regulated hydraulic pumps, which drive bending tables via a separate pressure cycle.
Just in time – Time as a scarce resource
Today, the processes in the producing industry need to be conducted faster, more cost-effective and more individualized. Saving only a few seconds has a definite effect on the production efficiency. The resource time, together with the material input, plays a decisive role in large-scale production. The central question for mechanical engineers therefore is:
At which point can technical improvements be conducted, to save time in addition to material? For faster tool change, Schwarze-Robitec has, for example, developed the rapid clamping system “Quick Tool Unlock.”
It consists of a split tension rod with clamping lever as well as a swivel device. Whereas in the case of standard market models, the continuous tension rod to the swivel arm crossbeam needs to be unscrewed at the top on the bend former for tool change, the procedure is much simpler with the Quick Tool Unlock: In this case only the clamping lever is actuated and the connection to the swivel arm crossbeam is separated. Then the swivel device can be opened, so that the bend former is exposed to the top. In interaction with the automatic tool clamping, the bend former can be removed without difficulty and without unscrewing anything. Long machine downtimes, due to complicated conversions, can therefore be reduced significantly. A relief which is of benefit to the operator because he can attend to his core tasks. If different radii or whole tube systems are to be produced, it is recommended to equip tube bending machines with multi-radius bending tools. With these, set-up times can be reduced by up to 70 percent and at the same time the utilization of the machines increased. Such time advantages pay off to a particular degree in the production of large-scale series. Thus also in the fast-cycle vehicle construction, more precisely in the production of complex bend in bend systems for exhaust systems. Especially suitable for this purpose are, for example, the CNC MR series bending machines from Schwarze-Robitec fitted with stacked tooling. They enable production of exhaust pipes with a bending radius of 1 x D without bending straight intermediate lengths between two bends.
Thanks to the stacked tooling, the set-up times are minimal.
Time-efficient design of work steps
CNC controls, which can run individual procedures simultaneously where possible, have been available on the market for some time already and help to save valuable seconds per production process. While developing its new machine control, the bending specialist from Cologne took this concept a decisive step further. It prepares the respectively following work step already while still carrying out the current procedure. An example: While the tube is fed to the tool, the clamping functions close almost completely. That means that the tool is immediately ready for the next bending step when the tube reaches its target position. Major productivity increases can be achieved in this fashion. In addition, it was very important for Schwarze-Robitec to develop a simple, intuitive and labor-saving control. In the past years, the number of machine functions has increased strongly. The integrated diagnostic and maintenance tool guides the operator through all setting and optimization steps, checks all data reliably for validity and so leads to an optimal production result.
Automatic bending cells
During cost-effective serial production of injection lines, cooling water and axis tubes, tie rods as well as various bodywork, exhaust system and chassis components it is worthwhile to expand machines to a fully automatic bending cell. They allow a completely automated production of bent tube systems: from the tube separation and welding seam positioning via the bending process all the way to integrated quality controls, bending or separating systems, as well as the further transport without personnel. Bending cells simplify and accelerate not only the machining process but also offer a high degree of operational safety. Designed for durability, the machines “Made in Germany” have no problems in coping with the two to three-shift operation and therefore not only have a positive effect on the productivity but also on the resource of money.