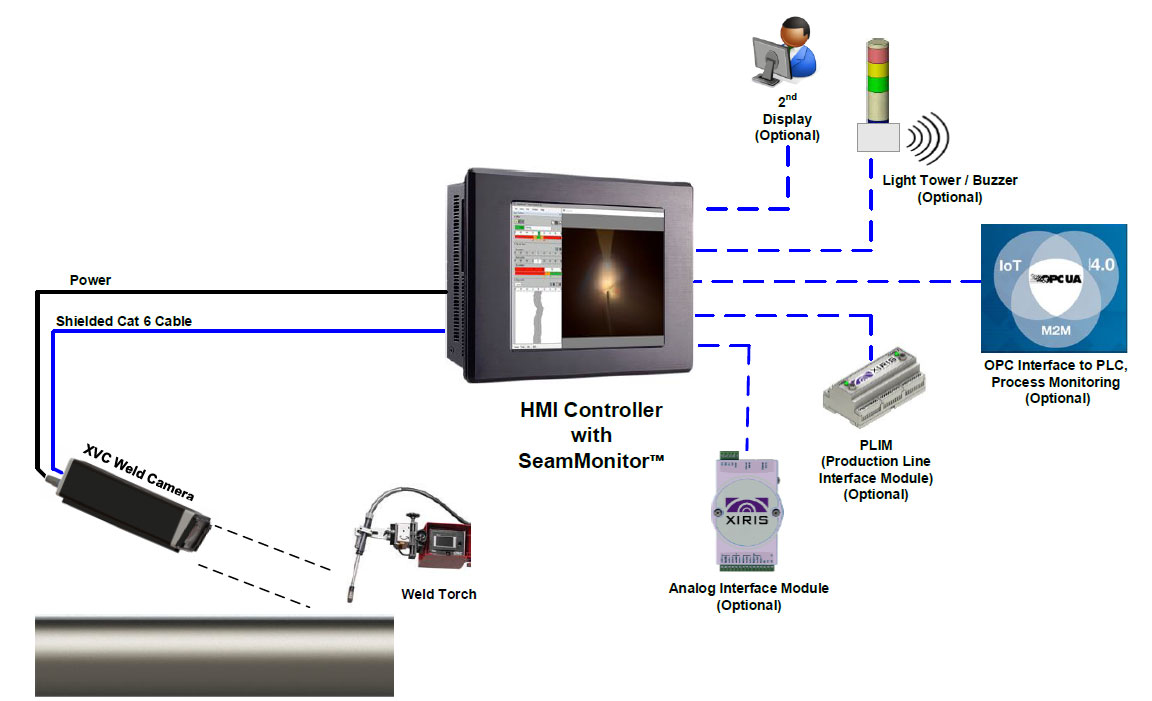
Xiris SeamMonitor™ System
Tracking the alignment between the welding torch and the weld seam is crucial to ensuring optimal weld quality in any seam welding application. This has been traditionally been done using a dedicated sensor using Laser Vision Triangulation (LVT) technology. Such sensors only provide an image of the laser line and provide no visual information of all the key details of the welding process that operators would like to monitor and control, such as the width of the weld seam, the melt pool size and torch tip condition. A view of these items would help to dramatically improve efficiency and productivity in tube production processes.
Even automatic in-process seam trackers are often subject to limitations that may allow automatic processes to go off seam. Post- weld non-destructive inspection technologies are performed too late after the welding process to allow operators to prevent misalignment and other welding related errors during welding.
However, with recent advances in electronic technology, it is now possible to get a good image of the weld arc and its immediate environment AND perform seam alignment all in the same camera device with the Xiris SeamMonitor™ system, a weld monitoring and alignment system that has been developed to reliably measure the alignment of the weld seam relative to the torch tip, the width of the weld seam and the torch tip condition. >The SeamMonitor™ system is a valuable process control tool that automatically alerts the operator when out-of-tolerance weld conditions occur, such as torch to seam alignment, seam gap width or torch tip quality degradation as well as providing a good quality image of the weld arc and immediate environment for process monitoring.
The SeamMonitor™ system provides operators two items in one: a high-quality, real-time image of the weld process that allows operators to see the condition of all the components in the weld area and adjust the process as needed; and an automatic seam monitoring system to automatically alert the operator or related machinery when the torch moves out of alignment to the weld seam or torch condition degrades.
The intuitive system enables the operator to set multiple warning and alarm limits that can integrate with other automation and notification devices. All parameters and images can be recorded for process monitoring and quality assurance based on the set-up parameters and defined warning limits.
It also provides a seam width and position movement history for process monitoring. Lastly, the system helps enhance operator and welder safety by removing the welder from the weld area, improving their productivity and working environment. The SeamMonitor™ System includes a high dynamic range (HDR) camera system, configurable optics that can be adjusted to suit most welding environments, an Industrial Panel HMI controller for image recording, processing and display, and image processing software for monitoring all details of the welding process, and optional features such as a Light Tower/ Buzzer to warn the operator of failure conditions or errors. The results of the system’s measurements can be used to control external equipment through a set of analog outputs which is also mirrored on the system display, or via a light tower.
By using the Xiris SeamMonitor, operators can obtain seam alignment and other simple weld inspections as well as having a clear image of the weld arc and its immediate environment to allow for weld process monitoring and ongoing adjustments to the weld process.