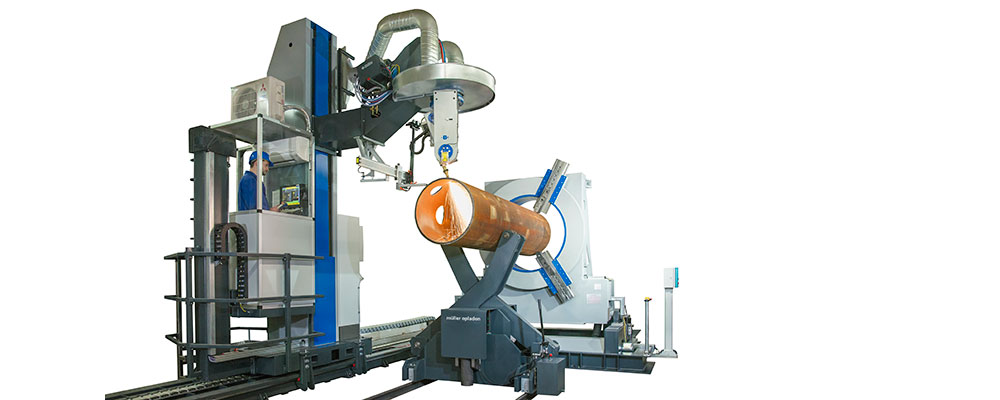
Two in one for a factor of 10
Combined cutter for pipes and dished ends from Müller Opladen
Until now, the cutting of pipes and dished ends has called for two distinct processes performed on different machines. Specialist Müller Opladen has now designed a combined cutter that scores with huge time savings and high production quality. Customers report a 10-fold boost to productivity.
The rationalization pressure in machine manufacture continues, particularly among manufacturers of high-grade technology competing in the marketplace repeatedly with suppliers in the low-wage sector. “At a customer’s request, we investigated ways of combining our 3D cutting equipment for the processing of pipes and dished ends,” Ralf Hamacher, Managing Partner of Müller Opladen, recalls. At the time, there was no machine available on the market that was capable of doing both jobs in a single system.
In the following months, the experts at Müller Opladen had to decide, for example, how the very different workpieces could be handled by one and the same clamping system. The key issue is that the centre of the cutting head always has to be aligned with the centre of the workpiece. “We achieve this with a self-centring 3-jaw chuck,” Hamacher explains. When cutting round pipes, the chuck is vertically aligned. To cut dished ends, the chuck turns hydraulically through 90° into a horizontal position.
After building the prototype and exhaustive field testing on the customer site, Müller Opladen developed a complete series for processing pipes and dished ends with diameters ranging from 1,000 to 3,000 mm. Tank holes with diameters of 50 to 2,000 mm and pipe connection pieces with diameters of 50 to 2,000 mm are achievable.
What this combined unit is capable of is illustrated by a practical example: the manual marking and cutting of a dished end with an 800 mm diameter and 6 holes takes 8-10 man hours. Handling the same tasks, the Müller Opladen machine slashes processing time to a mere 1 to 1.5 hours.
6 CNC-controlled axes in motion
The pipe profile cutting machine works with 6 CNC-controlled axes whose motion and speed are mutually adapted during the cutting process. This ensures the accurate positioning of the workpiece in relation to the flame cutter in order to achieve precision cutting results.
The axes are assigned to the various machine components :
Chuck: fixes the workpiece and rotates it about its own centre axis.
Torch carriage track for horizontal displacement of the flame cutter along the component’s centre axis
Lift column for adjusting the cutting head to the pipe diameter and for height correction during cutting
Boom with integrated horizontal and vertical swivel axis for adjusting the cutter during bevel cutting
Cutter retractor for the precise positioning of the cutter in relation to the workpiece surface during bevel cutting
Other components of the pipe profile cutting machine include the tracing system for pipe measurement and the pipe carriage for supporting the pipes during cutting.
Oxyfuel or plasma cutting
Müller Opladen offers cutting not only with oxyfuel but also with plasma. When using oxyfuel on wall thicknesses up to 150 mm, cutting can be performed with acetylene or natural gas. Bevel angles of up to 70° and tapers up to 80° are achievable.
For thinner-walled workpieces up to 80 mm, the user can use plasma cutting as an alternative distinguished by higher cutting speeds and superior cutting quality. Furthermore, plasma can also be used for reliably cutting stainless steels. The only limitation for plasma is its lower bevel angle not exceeding 45°.
Straightforward process
When the pipe or dished end has been clamped – clamping is automatic and self-centring – a laser measuring system scans the workpiece surface. This is a way of ascertaining the levelness of the workpiece in the area where the contour is to be cut. The differences in height caused by curved workpieces when rotated are measured and compensated for during the cutting process by variations in cutter position. Thanks to the self-centring clamping of the workpieces in the chuck, the zero point for dished ends is automatically determined, so no time-consuming measurement is necessary.
The data for each cut are transferred by a macro-based software system, specially developed by Müller Opladen, straight to the CNC axes. Data input into the software is possible online at the machine itself with parameter input, offline at an external workstation or by means of CAD data conversion. On the nesting principle, many process cuts can be performed in succession in a sequence that optimizes material usage.
Direct application of inscriptions and markings
The machine can be equipped with an integrated printer that communicates with the machine’s measuring system. By means of the machine’s position data, the printing head attached close to the cutting head advances into various positions on the pipe or dished end to apply inscriptions or assembly markings. The assembly markings are very helpful for subsequent welding of the connecting pipes or other components. The marking system can also adopt data from CAD systems.
Productivity up to 10 times higher
“Customers that are now using our hybrid machine have reported the huge benefits of the machine and anticipate rapid investment payback within two years,” says an enthusiastic Managing Partner Hamacher. “A customer in the USA has calculated that our machine has boosted his productivity tenfold compared to the manual cutting of dished ends and the associated connection pieces.”