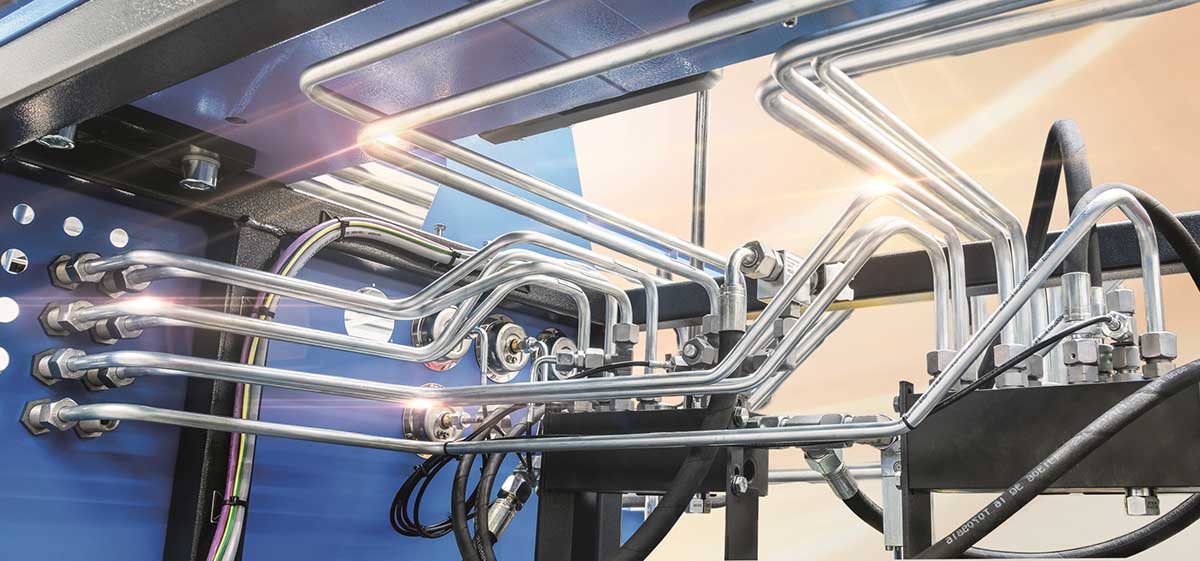
PIPE BENDING SYSTEMS: Trendsetter in the field of digital transformation
Networked tube and pipe production – global data flow
Improved quality and high added value – PBS-Systems proof their economic efficiency
The quick and easy manner to produce a flange tube
“In tune with the digital transformation”, this slogan of the scheduled International Sheet Metal Working Technology Exhibition has been taken literally: Concerning the fourth industrial revolution “Industry 4.0”, the PIPE BENDING SYSTEMS (PBS) division of TRACTO-TECHNIK GmbH & Co. KG in Lennestadt (Germany) presents itself as leader of the branch. As example the global player PBS introduces system solutions in the field of pipe assembling which are based on a continuously accompanying digital data flow from the draft stage up to the shipping of the finished tube; i.e. the standard “Industry 4.0” has been implemented in an exemplary way.
PBS had once been founded as a mechanical engineering company, but developed to offer intelligent solutions for all production steps of tube and pipe manufacturing and to get on top of the international league in terms of digital transformation. Today the modular extensible manufacturing system from PBS, composed of CAD interface and measuring technique as well as PIPEFAB software and pipe bending machines, is used around the world in many different fields of application to produce even customised pipes at a cost and quality level which otherwise can only be reached by mass production. Food, beverage or pharmaceutical industries, chemicals, bio-technique or air conditioning, at the shipyard, on a power plant construction site or if the assembly of hydraulic units has to be carried out: PBS systems stand for economical manufacturing, the perfect cooperation of the modular components offers potential savings up to 70 percent.
Directly after the transfer of the design and engineering data from the CAD system the PIPEFAB software controls the entire stages of production – from the material procurement at the very beginning to the final shipment of the finished pipes. Not only the generation of work schedules and production batches as well as the calculation of production times and production costs are based on the stored pipe geometry data; the warehouse management, withdrawal of material, pipe preparation, cutting to length, bending, deburring, welding and quality assurance operations (x-ray inspection, pressure test, etc.) are also derived from this information. No matter where around the world the measurements are taken, the design and engineering data is generated, the bending machine is situated, and whether the pipe segments are manufactured in series or individually: every single piece fits at the first attempt.
SCOPELINK and ROBOFIX: Measuring, welding, assembling – done
Another major highlight which has been developed by the PPS research engineers is the worldwide unique measuring system SCOPELINK for the frequently during pipework installation required adapter pipes. The use of SCOPELINK reduces the commonly time and cost intensive manufacturing of adapter pipes considerably: within only a few minutes the isometry data of the pipe layout can be precisely measured and stored. To save time, prefabricated pipe segments can be tailored by the software to meet the particular conditions of the installation on site. After the data transfer to the workshop or the PIPEFAB software the adapter pipe can be manufactured immediately.
The measuring operation includes precise gathering and documentation of the adapter pipe isometry as well as the position of the flanges and their hole patterns. Based on the pipe isometry the adapter pipe is bent or assembled of segments. For exploitation in the workshop the TRACTO-TECHNIK development section has designed another advantageous tool: the automated positioning unit ROBOFIX. To ensure easy tacking and butt welding this component allows fixing two flanges with their hole patterns in exactly the same position as they will assume after their final assembly. Additionally, the data required for bending and flaring operations can be generated directly from the pipe isometry.
High-quality mechanical engineering: Know-how and expertise
Substantially revised, completely modular structured, functional and ergonomically designed – but still as rugged and reliable as appreciated by the users: As technological pioneer in the field of tube machining the latest generation of the tube working centre TUBOMAT sets its own particular standard. Independently of complex controls by digital information professional and high-quality mechanical engineering remains the key for precisely manufactured tubes of all possible dimensions.