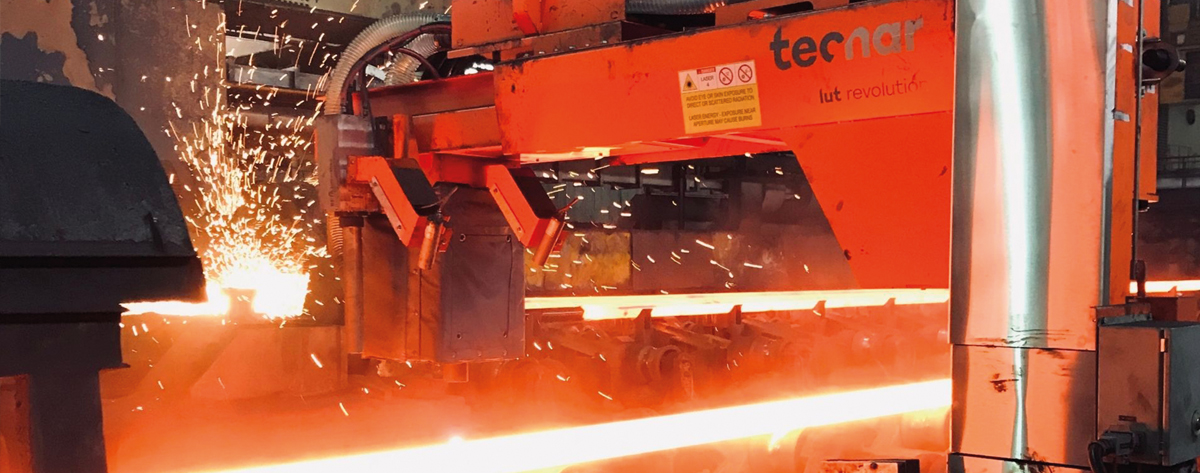
Mastering seamless tube quality: How laser-ultrasonics reshapes non-contact hot tube measurement
Introduction
In an ever-evolving economy, tube and pipe manufacturers are facing unprecedented pressure from increasing client expectation, fierce competition, and intricate, unstable supply chains and rapidly rising inflation. Internal pressure is also considerable as companies constantly look for ways to reduce costs, improve quality control and increase productivity.
Early insight changes everything
To counter this unpredictability, manufacturers must accurately control product characteristics and quality from the first production stages.
Consider, for instance, the importance of the earlier detection of uneven heating in billets, unavoidable tool wear or of drifts in roll-stand settings. Each mill variable has an impact on the characteristics of the finished product. In the harsh environment of these mills, unpredictability lurks at every step of the production line. Knowing about the performance at each stage of the process is crucial to controlling output quality and loss reduction. The challenge is to do so online and in real time when the tubes and pipes are hot and being formed.
The good news is that there are hot production line optimization tools to help achieve these goals.
Gamma ray gauges have long been a mainstay in the tube industry, but their prevalence is marked by unremitting constraints. Gamma ray emitting sources, such as the radioactive isotope Cs-137, are subject to increasingly stringent regulations for their acquisition and replacement, making this technology even more difficult to manage. What’s more, geopolitical factors constantly threaten supply to and embargoes, currently the case in some countries. As the industry grapples with these limitations, a proven, viable technology is earning widespread attention: laser-ultrasonics.
Tecnar’s Lut 2.0 is at the forefront of this technological transition. This non-contact gauge is designed to measure the key online characteristics of hot tubes and pipes during manufacturing, such as wall thickness (WT), eccentricity, temperature, and length. The Lut 2.0 may be used from billet piercing outlet to sizing mill outlet. By monitoring key tube characteristics and using its innovative algorithms, the system automatically tracks slow drifts in production and their cause before they deviate from finished product specifications. All of this means that operators receive early insights so they can pre-emptively fine-tune parameters and implement corrective measures on time, optimizing production and quality.
How the Lut 2.0 achieves this:
Operating in tandem with the plant network, the Lut 2.0 requires a minimal set of inputs: the tube's nominal WT, nominal outer diameter, and alloy type. With this information, the gauge automatically sets the precise position of the measuring probe, plus the proper speed-of-sound chart from the integrated database tailored to the alloy and measured temperature. From there, the intelligent algorithm is set up to process and interpret the recorded laser-ultrasonic waveform, uncovering any WT or eccentricity anomalies. As the Lut 2.0 deciphers each tube's story and tracks drifts in long production runs, it synergizes human experience and machine precision.
Real-time data:
Real-time information is crucial for monitoring dynamic processes. Lut 2.0 collects highly accurate real-time data essential for tracking batch trends and progressing potential WT and eccentricity deviations. These may be caused by uneven heating of the billet, by inaccurate roll-stand settings or by tool wear. Using the detailed automated analysis of a tube sequence’s WT profile, the Lut 2.0 identifies and tracks the source of deviation. Operators then receive the results in a comprehensive and intuitive user interface.
User-friendly interface (UI):
Organized in an intuitive architecture, the information is presented in the form of tables or graphs by a user-centric interface (UI) based on a powerful software platform. The UI displays information such as pipe identification and characteristics, illustrations of pipe radial and longitudinal profiles and batch history in Windows or in the same screen, as the user prefers. Easy-to-interpret visuals deliver valuable information at a glance. Its intuitive design minimizes the learning curve so that users can easily use the software's various powerful features. In addition, an easy-to-navigate dashboard allows plant operators and managers to quickly access the information, providing them with a gateway to agile decision-making.