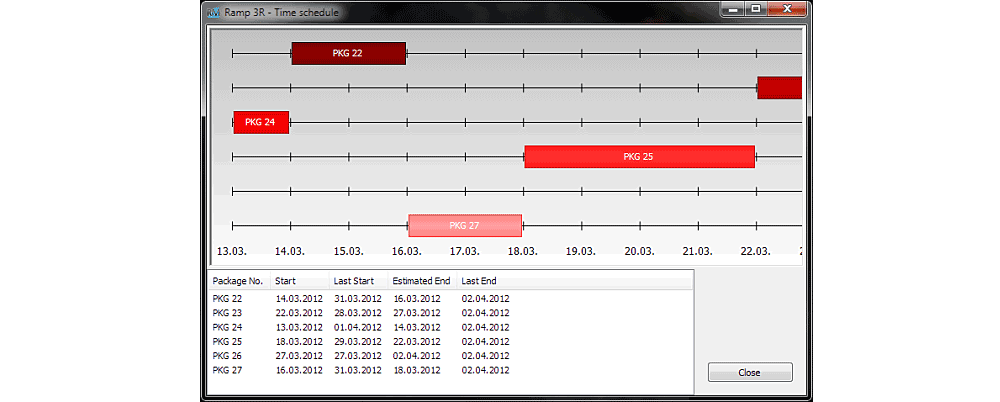
Software for Pipe-Spool Prefabrication
Pre-fabrication of pipe-spools, whether for the oil and gas industry, ship building, automotive or the aerospace industry involves more than just the operations on the shop floor itself. While the actual fabrication processes are of course the most visible, and the associated costs can be calculated relatively easily, there are a number of other processes and cost factors, which are not as readily apparent and not as easily quantified.
These factors include the work-preparation (creation of work packages, BOMs, allocation of jobs to specific workers) as well as fabrication supervision (logistics and material handling, revision management, status tracking, quality control, report and documentation generation). In combination the costs associated with these tasks can easily match or exceed the costs for material and workers. This is because on the one hand the people handling these jobs are highly paid engineers, and on the other hand problems or delays here will significantly impact shop floor operations, causing idle times at the machines, bottle-necks and material wastage.
3R solutions from Germany is a specialist for pipe-shop automation and integration, which includes providing an integrated software suite. By covering the entire process chain from the 3D model to assembly and installation, pipe-shop owners can prepare optimized work packages, track the status of each spool (including the entire history of each welding joint), and generate all required documentation both for fabrication itself as well as for tasks such as productivity or cost calculations, QC reports, or revision histories.
The heart of the software suite is the integrated database, which includes information on every component (pipes, fittings) that is used in fabrication, mapped to the database of the customer’s CAD software. By utilizing a PCF or IDF interface (other interfaces can be implemented if necessary) the 3D models can be imported and are automatically converted into isometric drawings. If spool breaks are already included in the 3D model, these breaks are imported as well, otherwise the software can automatically split the line drawing into spools according to customizable parameters. In addition all required BOMs, cutting and welding lists and a number of other reports can automatically be created from the drawing.
When a drawing is released for fabrication, the software calculates the required capacity utilization, and can check for material availability and installation schedules, as long as these are available in digital form (e.g. by interfacing to the ERP system or by receiving a regularly updated spreadsheet with this information). Based on all these data the software then can create optimized work packages, which (among other benefits) reduce cutting scrap and balance the workload evenly among all workers (especially fitters and welders). Since the workload for each worker is known ahead of time, this also allows for streamlined logistics, because material can be delivered directly where it is needed, rather than having operators leave their stations to get the material they need.
By adding computer terminals to each work station it is also possible to not only achieve a mostly paperless workshop (since all work orders are displayed digitally), but to track the fabrication status of every component in the shop, giving full traceability at all times. By adding various other data, such as an operator ID it is also possible to create a comprehensive joint history from fit-up through welding and inspection all the way to on-site installation.
The great strength of the 3R software suite is that the developers always try to consider the specific needs and requirements of the customer. By listening to their feedback and ideas, they can deliver a software that is at the same time very user-friendly and intuitive but also customized and powerful to meet the demands of the operators. In combination with a 3R designed automated pipe-shop, it is possible to significantly reduce operational costs, while streamlining the data flow and the fabrication processes, in order to have an efficient and highly productive workshop.