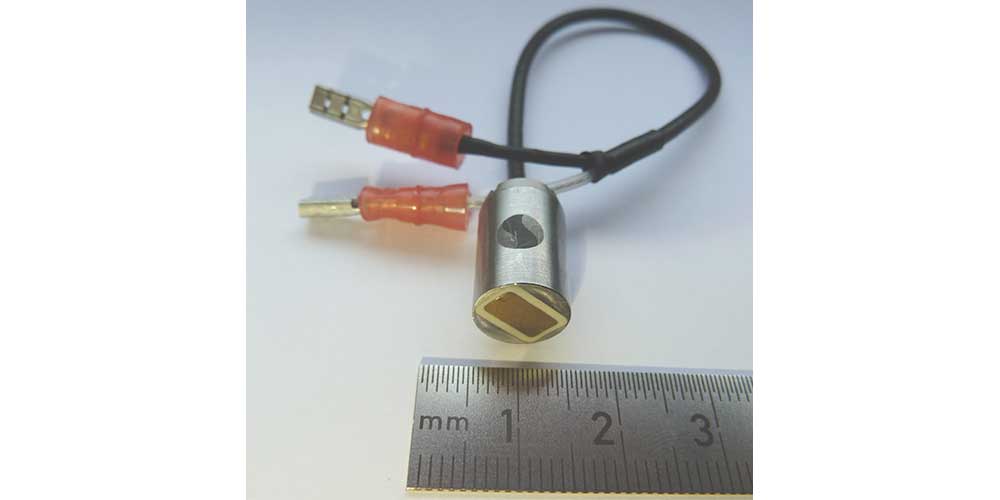
Slickers unveils ultrasonic transducers for detection of defects in the micron range
The most critical part for any ultrasonic test system is the transducers used for defect detection. The transducers are the “ears” of the non-destructive acoustical testing equipment, and arguably the single most important component in a UT system. “Being hard of hearing in the transducer world is not a good thing, deaf ears will not do the job nor can you do anything to cure them it has to be well designed from the start with application specifics in mind” Klaus Dickmann, Slickers head of NDT points out.
When Slickers developed their UT electronics and software package three years ago to match their industry leading mechanics, transducer development was also one of its main priorities. “If you start with a noisy signal because your transducer isn’t performing to peak you cannot improve anything in later stages and the whole system will not perform!” Slickers NDT engineering team carefully looks at each customer’s application and works with them to develop the best transducer possible for their application and defect size to maximize the line rate capability.
Nevertheless, as pointed out in Terry Banach’s series of articles about UT testing in this journal, it is not sufficient to only have great transducers. “For reliable testing of defects with the depth of down to a third of the diameter of a human hair you have to have a complete system that can work very accurately” is the NDT specialist’s conviction. “It’s always a challenge to achieve what is close to the limits of physics under industrial circumstances. This can only be realized by a meticulously designed system starting with very precise mechanics, tube guiding, coupling water system, transducers, matching UT electronics and software. This is Slickers strength, we take care of all the details with our engineering teams to deliver turnkey ready systems to our customers”.
Slickers recently proved highly repeatable results using reference reflectors as small as 25 micron deep and as short as 500 micron in length could be detected in Zircalloy, titanium and stainless steel tubes. With their latest release of application specific transducers for the Rota25 they have greatly improved the capability of the industry standard for nuclear and aviation tube testing. The German based UT supplier takes accountability for the quality of its transducers both for standard and custom developed applications and will supply certification according to international standards like the EN12668-2. We are able to characterize and certify our transducer designs and we also offer annual or semi-annual recertifications of existing transducers for customers requiring this to meet the end customer’s quality needs.