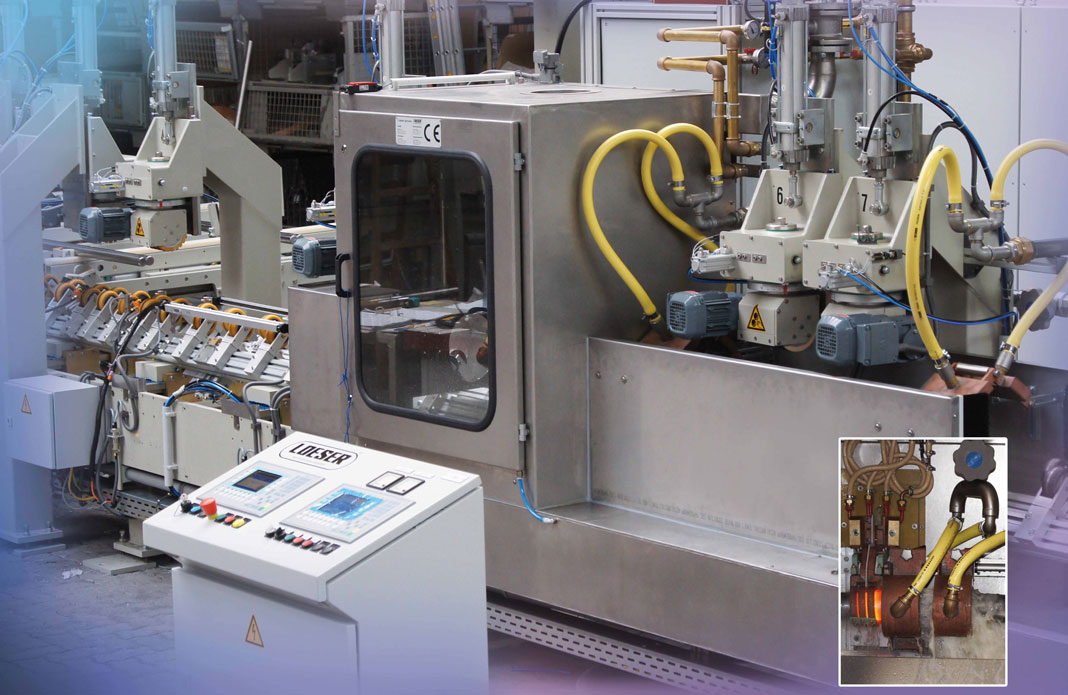
Innovative through feed induction hardening
Hardening of the surface is necessary for work pieces exposed to severe work conditions such as hydraulic cylinder rods on earth moving equipment. This process makes the surface much more resistant to scraping, gouging, and denting caused by hard objects striking the outside diameter.
This process is mainly used on hydraulic cylinders; other applications include ball screws to increase the wear resistance in the ball track and other round parts
The technology is based on the induction hardening process. Induction hardening uses eddy currents to produce heat on the surface of the work piece. Eddy currents are evoked by one or more induction coils with high frequency alternating current.
The number of induction coils used, is determined by the required through feed speed, depth of hardness and the diameter of the bars or pipes.
A continuously running transport system feeds the steel bars through the induction coils at a consistent speed.
Specifically engineered transport system, controlled by the PLC, is designed for maximum efficiency and production. The extremely accurate and repeatable spiral movement insures consistent hardness and hardening depth throughout the complete bar.
The outer surface heats up to the required hardening temperature. Deeper layers will not reach this temperature during the short heating period and therefore will not be hardened.
Immediately after heating, the bar or tube is quenched with an emulsion or with water. The quenching medium is applied by an automatically operating quencher.
A quantity of bars is initially loaded onto a load table equipped with an automatic operating magazine loader. The magazine loader picks up the bar and places it onto the in feed transport conveyor where it then travels through the hardener and exits the machine on the exit transport conveyor. The bar is then automatically lifted off the exit transport conveyor and placed onto the unload table. The process automatically repeats leaving the minimum amount of distance between bars for maximum efficiency. After quenching, the residual cooling agent is removed from the bars using an air blow off device. The guide roll system moves the bars to an ejector. The bars are retained in an outfeed magazine. The effective hardening depths depend on the required operating conditions. It is possible to reach a depth of approx. 2,5mm. Hardening results also depend on the material up to 700 HV/60HRC. Depending on application these values may vary. Additional induction coils allow further hardening depth. Depending on the hardening temperature it is possible to vary the surface hardness. Throughput speed varies depending ont the diameter of the part. Smaller diameters feed faster than larger diameters proportionetly.
Once process parameters are determined that produce the required hardness, hardness depth and production requirements for each bar, all parameters are then stored on the PLC and can be easily retrieved the next time this bar is processed. The work pieces can be moved manually or automatically to the next production machine, which is usually a straightenier.
After the straightening process (if required) bars are polished to the required surface finish parameters using a multiple station abrasive belt polisher. A bonded wheel (stone wheel) grinder is in most cases not capable of producing adaquate surface finish parameters required for chome plating ultimately effecting the life of the piston rod seals on a hydraulic cylinder rod.
After the straightening process (if required) bars are polished to the required surface finish parameters using a multiple station abrasive belt polisher. A bonded wheel (stone wheel) grinder is in most cases not capable of producing adaquate surface finish parameters required for chome plating ultimately effecting the life of the piston rod seals on a hydraulic cylinder rod.
This processing step is preparing the workpiece surface for the chrome plating. The processing of the surface could be quickly and automatically implemented with Loeser belt grinding systems.