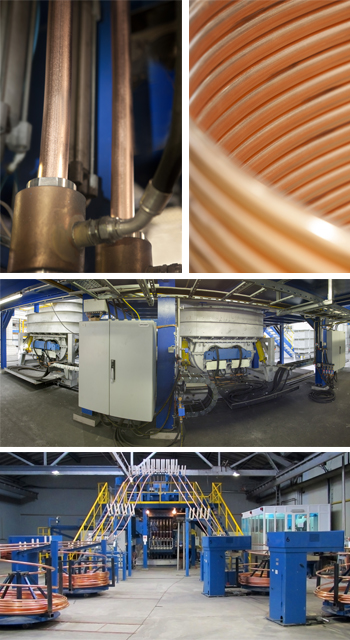
UPCAST®-SGTube continuous casting technology is our expertise – let us find the right solution for your needs
UPCAST OY is a supplier of UPCAST®-SGTube production lines for upward casting of thin-walled Cu-DHP tubes ready for further processing into various high quality tube products.
UPCAST®-SGTube continuous casting technology offers a shortcut in copper tube production process getting you there in one-step compared with the traditional multi-step tube production. It is an innovative extension of the UPCAST® system used for casting Cu and Cu-alloy rod sharing all the same inherent benefits of our standard system, with specific construction of the casting machine, coilers and casting machine tooling.
The UPCAST®-SG cast tube has a fine grain structure allowing for its straight breakdown drawing followed by inductive in-line annealing. To ensure complete softening a total area reduction of min 50% is required before intermediate annealing.
UPCAST® rod and UPCAST®-SGTube lines are both of modular design offering solutions for small and medium capacities. With a double-furnace configuration (separate melting and casting furnaces) it is possible to reach 12,000 tpy. Sizes of tube with outer diameters from 38 mm to 60 mm have been cast, with wall thicknesses of 2 mm/ 3 mm respectively. Different tube sizes can be cast even simultaneously when the casting machine is equipped with more than one servo-drive system. The smaller the final tube size, the smaller the cast tube size. With respect to coil weight UPCAST®-SGTube is extremely flexible with an upper limit of about 1.5 tons. The final weight limit is more likely to be determined by the downstream process equipment.
The main usage of UPCAST®-SGTube is in the casting of phosphor deoxidized (DHP) copper tube for the production of sanitary, industrial as well as ACR tubing. The process is however not limited only to DHP copper but is suitable also for other copper grades/copper alloys. Oxygen free copper as well as copper nickel alloys have all been successfully cast.
Having the UPCAST®-SGTube process as the first step of tube production line is extremely cost effective due to smaller energy consumption, which means clear savings to the lifecycle costs. All this with a small environmental foot print. It is also possible to use clean and dry scrap in the process with the double-furnace configuration.
Further savings can be gained through the smaller space requirement of the line. It is just a fraction of the floor area required by the conventional equipment, which can be replaced by the UPCAST®-SGTube line.
After the advent of UPCAST®-SGTube it was only a question of time before a hybrid system capable of casting both rod and tube would emerge.
UPCAST®-Hybrid technology is based on using the same equipment for casting both products and it is a perfect solution for the capacity optimization, a truly cost-effective solution for companies with a diverse product portfolio.
A hybrid configuration may have two separate furnaces from which the casting takes place. However at any given time just one will be used for casting purposes while the other would be in a standby position. Such an arrangement allows two different types of melt to be continuously available - e.g. oxygen free copper for rod and DHP copper for tube. Typically just one product type is cast at a time but the hybrid casting machine does allow also rod and tube to be cast simultaneously when produced from the same type of melt.
The hybrid solution is very good for the companies who have a certain capacity requirement for both rod and tube – no need to have two separate lines and in worst case neither one being fully utilized all the year round. With the UPCAST®-Hybrid line one can optimize the full capacity between both products or sometimes for only the other product.
The technology is the result of consistent UPCAST® R&D work, which is carried out by our experts at the company´s own pilot plant. The company is determined to stay on top of the development in its field and is continuously looking for improvements, new products and applications to meet the changing requirements of the customers and markets.
Production lines are never short term investments, but the customers are carefully planning their capital expenditures for years ahead. UPCAST® continuous castings lines are reliably and fully operating every day of the week. This would not be possible without a fast, reliable and continuous UPCAST® Customer Support for consumables and spare parts. The opposite could mean major losses through the lost production time for customers. We remain at your service – continuously! UPCAST® Quality will continue to be the best in the market.
UPCAST OY and Asmag GmbH from Austria have cooperated for some years joining forces to offer their customers an efficient Cast&Draw solution for semi-finished copper tubes. The “Cast” portion consists of the UPCAST®-SGTube process while the “Draw” part includes straight drawing and intermediate annealing equipment. The C&D production line requires much less space than the conventional equipment. Output from a single C&D unit is today possible up to 12,000 tpy. Adaption of the C&D concept to copper alloys is also possible one example being Cu-Ni tubes for seawater applications.
Come and see us at Stand No. 538 at TUBOTECH
in Sao Paulo in October 6 - 8, 2015!
1) Original UPCAST ® upward casting technology is based on carefully designed and manufactured parts and components
2) UPCAST ® SG cast tube in coil
3) UPCAST ® double furnace configuration is designed for bigger capacity requirements and is ideal also for the lines utilizing 100% recycled material
4) UPCAST ®Hybrid line capable of casting both rod and tube – excellent solution for optimizing the capacity