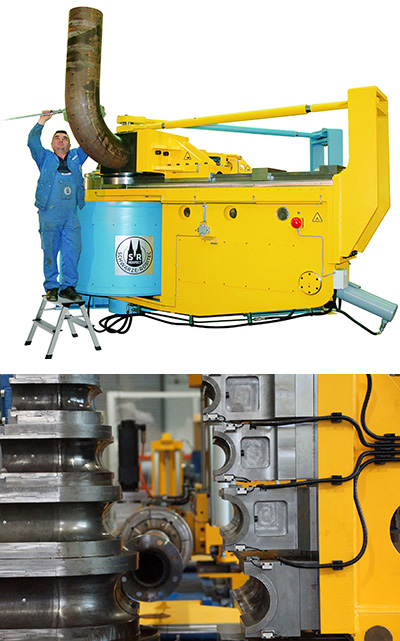
Fast and Precise in Chemical Plant Engineering
Within the next 8 years, investments in chemical plants will double worldwide based on the forecasts of the American Chemical Council (ACC). The reasons for this are the global mega trends such as population growth, emerging markets, and the appetite for raw materials. This increases the necessity for the plant designers to demand more machines that allow the time-efficient manufacture of enormous quantities of tubes. It goes without saying that this cannot happen at the expense of quality. This is not an easy task because the high-strength special materials – which are often flanged, beaded or double-walled tubes – require a demanding process.
There are two different production methods that have been established and are being used for chemical plants in order to manufacture tube systems: Welding of bent tube components or the production of complex tube systems by using bending technology. In order to fabricate tubing systems, many manufacturing plants commonly use welding procedures in order to connect straight tube sections with weld-in elbows. However, this procedure requires very time- and labor-consuming work steps: First, the individual tube components must be welded. Subsequently, each individual weld joint is subject to a costly inspection method that must guarantee the air tightness of the line. Considering the multitude of connecting points, this is a very labor-intensive procedure that may still contain the potential of making errors. The cold bending procedure reduces the required work steps to a minimum. Bending machines can form complex tubing systems from a single piece of blank. However, not every bending machine can guarantee compliance with the high demands the chemical industry places on the forming process. When selecting the right machine, one must verify that the machine is designed for bending stainless steel tubes and ensures the absolute minimum ovality when forming the tube. The latter is an important requirement for all tubes carrying chemical substances. Eventually, the tubes are cleaned using a spherical object that is slightly narrower in the center; it is referred to as a "PIGs" (Pipeline Inspection Gauges). Excessive ovality in these so-called PIG tubes can lead to chemical residues that become mixed in the next production loop.
The automatic CNC machines of the heavy duty series from Schwarze-Robitec GmbH are optimized precisely to meet the requirements of the chemical industry. They produce three-dimensional tube systems rapidly and exactly. The tube is clamped into the index head and positioned in the space by means of the transport unit and index head. After the first bend, it is directly pushed on and rotated, if required. Thus, three-dimensional tube systems with minimum ovality are produced that fit precisely.
Focusing on increased production rate
When the speedy manufacture of different types of tubes is important, CNC tube bending machines with multi-stack bending tools is a wise choice.
The multi-stack bending tools allow you to process tubes with different nominal diameters on a single system without retrofitting efforts. One of these systems is the CNC 220 HD MW of the HD series from Schwarze-Robitec. It bends tubes with a maximum diameter of 219.1 x 12.7 mm and a tube length of up to five meters. With the help of the multi-stack bending tool, up to 70 percent of the setup time of market-based systems can be saved. It is possible to process tubes of different materials, such as steel, nickel alloys, iron and stainless steel on one tool. Time-saving technologies are also available for the forming of double-walled tubes and flanged tubes. For example, Schwarze-Robitec offers flanged tube equipment that takes the flange and sleeve positions into consideration before the bending process starts.
The time-consuming subsequent adding of flanges in order to finished tube bends is omitted, and the tubes can be implemented into existing systems after the bending process is completed. Another “time saver” is marking devices which indicate the positions on the tubes where welds or bypasses are to be implemented after bending.
Smart ways to curb the cost
Long pipelines made of high-quality materials create considerable costs and quite often must be integrated in a space-saving manner. One option are small bending radii. They optimize tube runs enormously if space is limited and reduce the usage of material. For example, the CNC 320 HD from Schwarze-Robitec produces extremely small bending radii of 1.5 x tube diameter. This applies also to large, very thin-walled tubes with a diameter of up to 323.9 mm and a length of 6 m. Similarly tight radii with such large tubes are usually achieved only with warm bending processes or welding elbows – a process that is much slower and more expensive. In addition to a wide variety of CNC controlled machines, the company from Cologne, Germany, also produces semi-automatic systems. Machines such as the SR 320 are perfectly suited for the production of individual bends and small production runs. However, all models of the HD series have one thing in common: A very rugged standard machine with extremely high structural rigidity. It withstands the enormous bending forces. Based on the tremendous power reserves of its clamping forces, the machine produces optimum bending results.
Pictures in order of their appearance:CNC 320 HD MW
The CNC 320 HD from Schwarze-Robitec produces extremely small bending radii of 1.5 x tube diameter, including very large, thin-walled tubes with a diameter of up to 323.9 mm.
Focusing on multi-stack bending tools
With the help of the multi-stack bending tool, up to 70 percent of the set-up time of market-based systems can be saved.